Abstract: The difficulty of robot laser cladding processing for the processing of complex workpieces such as blades lies in the utilization of high–precision characteristics, and the technical architecture advantages of iRobotCAM based on 3D CAD kernel can effectively meet the requirements of high precision, so as to realize high–precision laser cladding processing of five–axis blades.
The design and processing of blades need to be adapted to specific scenarios according to different application scenarios, from small fan blades to aviation blades, according to the different application scenarios of industrial products, the design elements are different, some require beauty-oriented, some require silence-based, some require performance-based, and whether the blade finally meets the needs involves the needs of different industries, as well as the requirements of different process methods, the core is the control of precision, only the accuracy is effectively controlled, There is a way to meet the needs of different scenarios. Taking the robotic laser cladding processing of blades as an example, iRobotCAM takes advantage of its CAD-based architecture and has the advantages of high-precision architecture, how to effectively apply it to laser cladding processing?
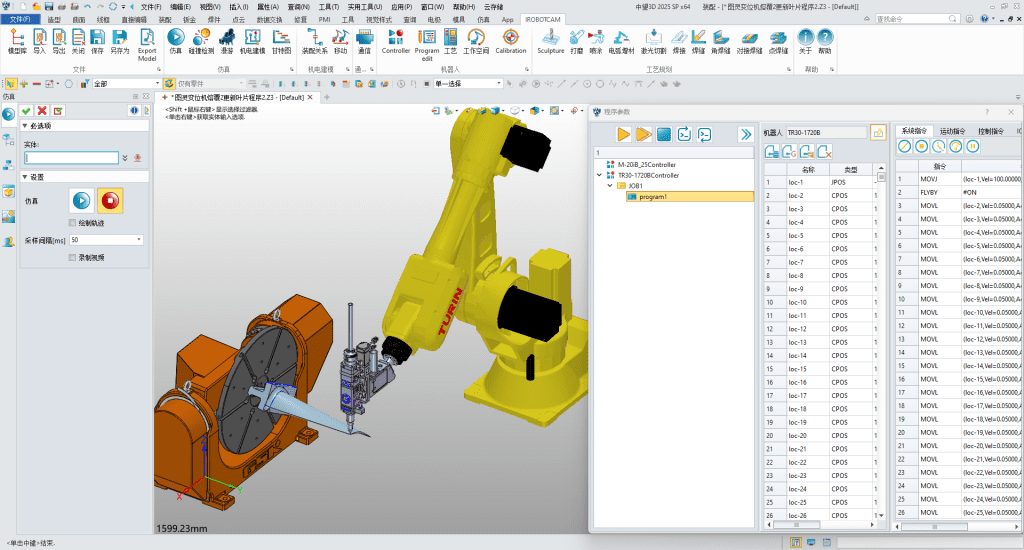
For robotic laser processing applications, the usual process is as follows:
Import robot and workpiece> positioning of workpiece and robot calibration> realize trajectory programming> simulation of all scenes> code output and robot processing
1. Using the characteristics of iRobotCAM based on the 3D CAD platform and looking at 3D, you can quickly establish a digital model of the robot application scenario
2. Using the electromechanical module of iRobotCAM and the preset robot library, you can define relevant robots, tools, etc. for the robot scene
3. According to the needs of the laser processing process, various 2-axis to 5-axis trajectories are generated to meet the trajectory requirements of specific scenarios
4. Based on the physics engine of iRobotCAM, the movement of the robot is simulated, calibrated, and the corresponding execution code is output.
In addition to the technical architecture, the most direct user perception is how easy the programming of the robot software is, and the user experience is one of the core indicators. Frankly speaking, the progress of industrial software is not a day’s work, but from the technical architecture to the user experience, domestic industrial software has made great progress in recent years, with so many years of foreign software, you may as well try domestic industrial software, for the choice of robot offline programming software, you may as well try iRobotCAM.
Taking the use of Turing robot to realize the laser cladding processing of five-axis blades as an example, how does iRobotCAM easily realize robot laser processing step by step? The following video can intuitively show the simulation of robot laser cladding processing programming and the ease of operation.
Contact us and get more robotics solution reference.
About Yueqing Technology
Yueqing Technology is committed to building an open iRobotCAM robot offline programming platform, which is a digital solution integrating electromechanical conceptual design of production lines, robot processing programming simulation, and virtual debugging.
iRobotCAM website: www.iRobotCAM.com, contact: cooperation@iRobotCAM.com