Abstract: Lasers have the characteristics of high precision, and how laser equipment can achieve high-precision applications involves not only the hardware precision of the equipment, but also the adaptation precision of the software. Taking robot laser processing as an example, the technical architecture advantages behind the iRobotCAM robot programming software can ensure high-precision adaptation.
Due to the high-precision characteristics of laser technology, various types of laser processing equipment have emerged to continuously meet the needs of various application scenarios. For the precision control of equipment, in addition to the debugging of related hardware such as lasers, software is also a key link. Taking robot laser processing as an example, iRobotCAM provides a comprehensive laser processing process module that can adapt to various types of robots. Through the advantages of its high-precision technical architecture, it can meet the processing needs of various high-precision or complex products. More specifically, what are the obvious advantages of choosing iRobotCAM as the robot laser process application software?
Technical perspective
- High-precision trajectory algorithm: Built on the robust ZW3D platform, this advanced algorithm leverages ZW3D’s diverse 2-axis to 5-axis trajectory capabilities. As a result, the robot executes trajectories with unparalleled precision, akin to that of CAM software during laser processing. This ensures that the laser beam is accurately focused on the targeted processing areas, enabling high-precision laser cutting, welding, and engraving. The outcome is a consistently superior processing quality, maintaining the same high standards throughout each operation.
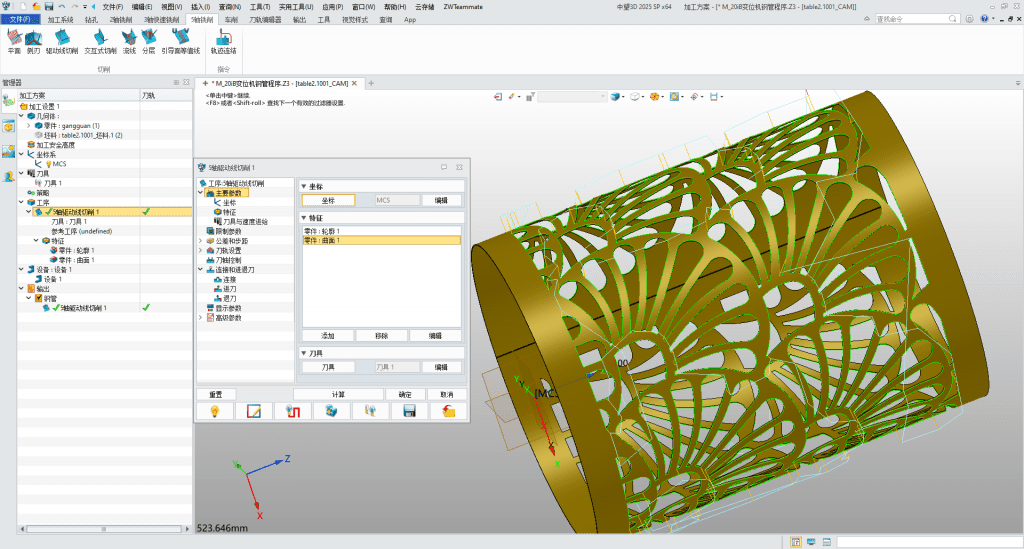
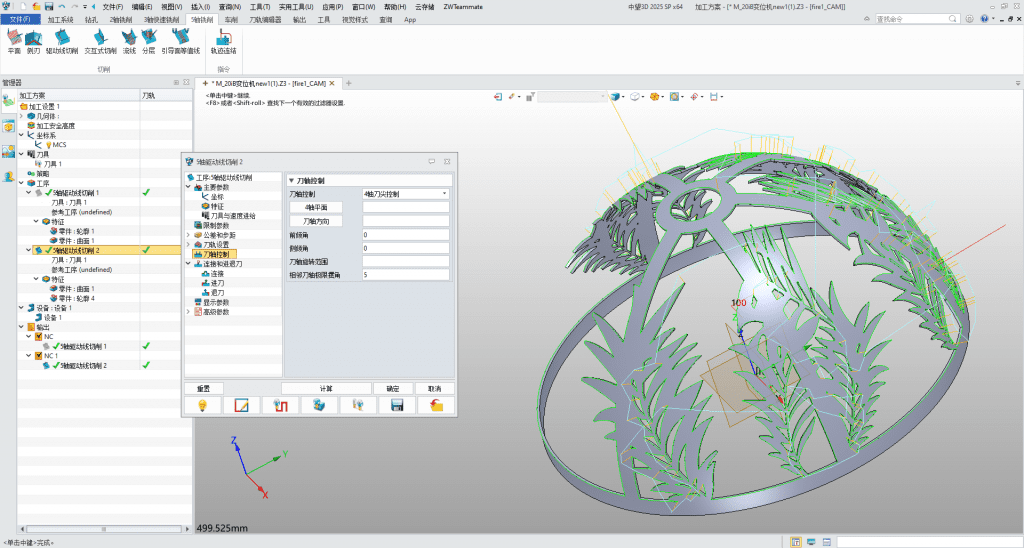
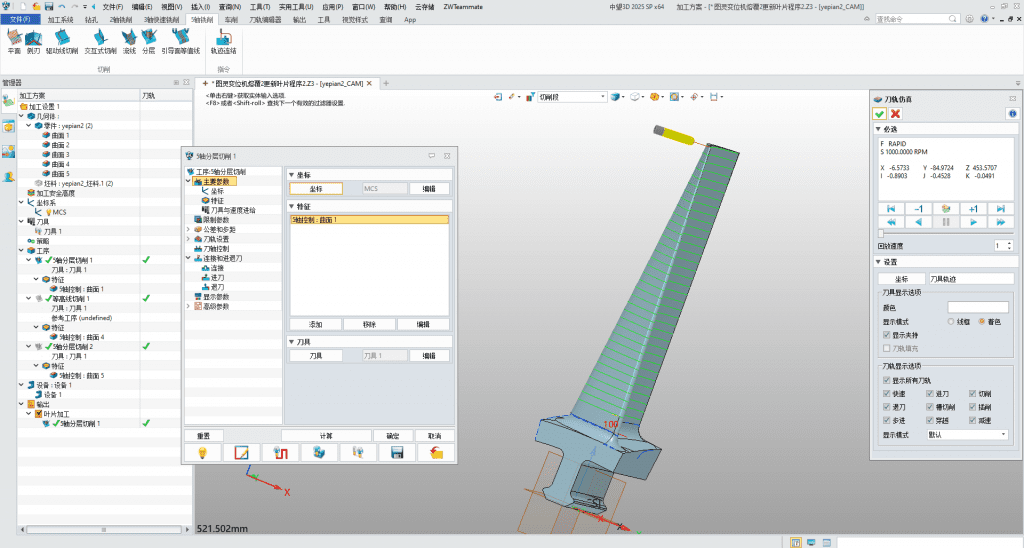
- Virtual debugging function: With a mechanical and electrical modeling module, it can model and design the production line and conduct virtual debugging of the robot. By simulating the laser processing process in the virtual environment before the actual production, it can discover and solve possible problems in advance, such as robot motion collision interference, checking robot singularity, accessibility and collision, and laser path errors, etc., so as to reduce errors and risks in actual debugging. Improve productivity and safety.
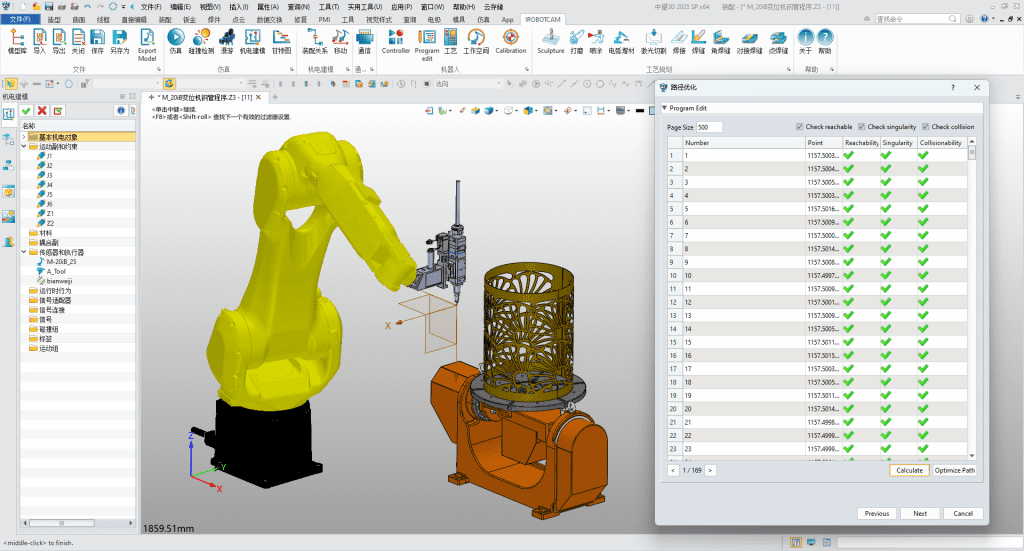
Efficiency perspective
- Fast programming and updating: iRobotCAM can quickly change the workpiece model and processing process requirements according to the actual needs, can quickly realize the update of robot programming, without re-carrying out the cumbersome programming process, saving a lot of time and energy, especially in the face of small batch, multi-variety production tasks, the advantage is more obvious.

- Efficient simulation optimization: After laser process programming, the entire processing process can be simulated, intuitively display the robot’s movement trajectory and laser effect, and optimize the processing path and laser parameters through optimization algorithms, further improve the processing efficiency and quality, reduce material waste and processing time.
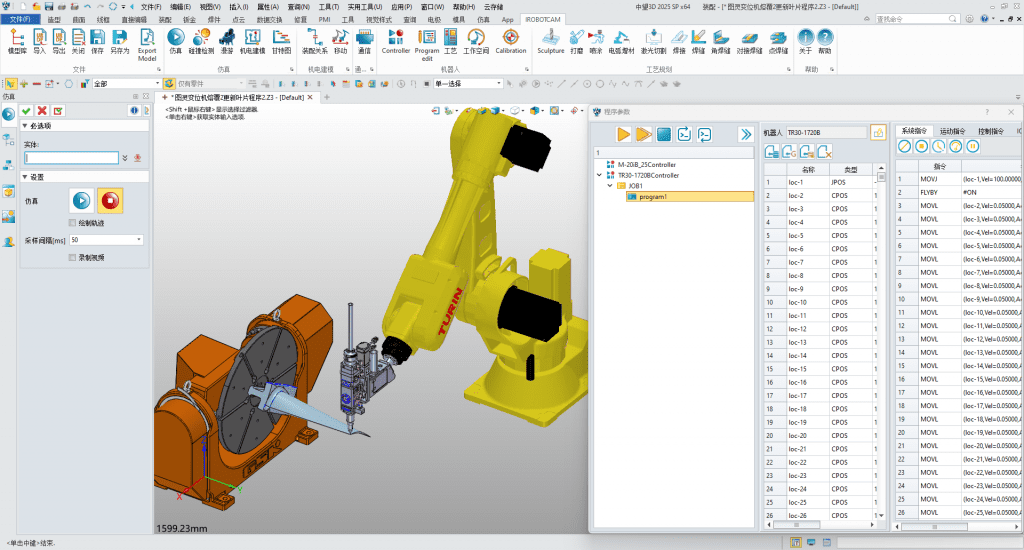
Compatibility and commonality level
- Support a variety of robot brands: With strong compatibility, it can support a variety of brands and models of industrial robots common on the market, such as Fanuc, Kuka, Yaskawa, etc., not subject to the restrictions of specific robot brands, enterprises have greater flexibility in choosing robots, and can choose the most suitable robot equipment according to their own needs and budgets, without worrying about software incompatibility problems.
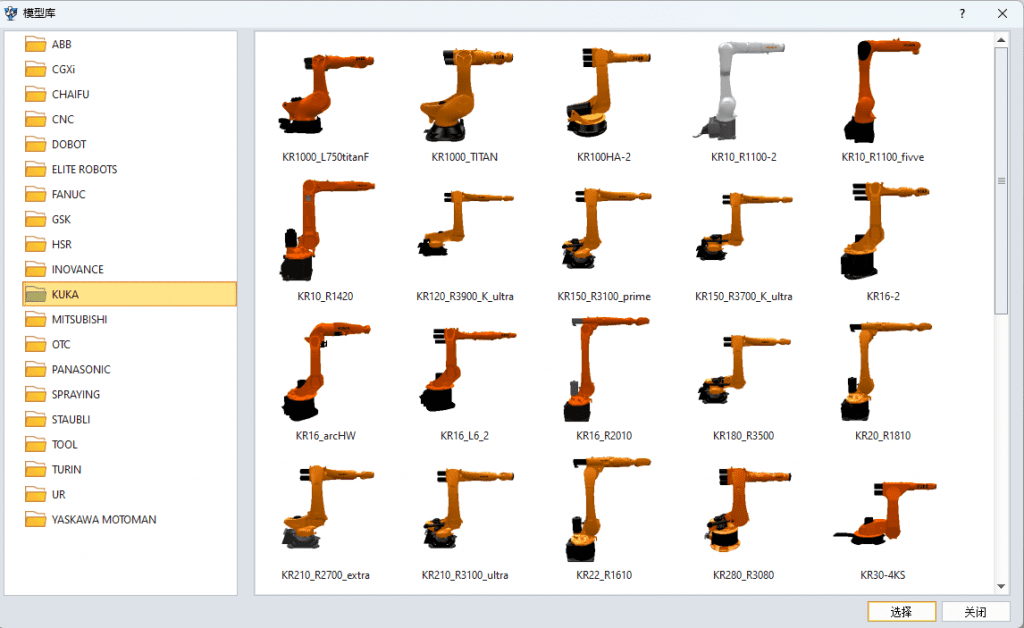
- Supports the import and placement of multi-format cutting parts into the model library: It can be imported and integrated with different types of laser equipment, and can be realized through iRobotCAM to work together with robots to meet the diversified laser process needs of enterprises.
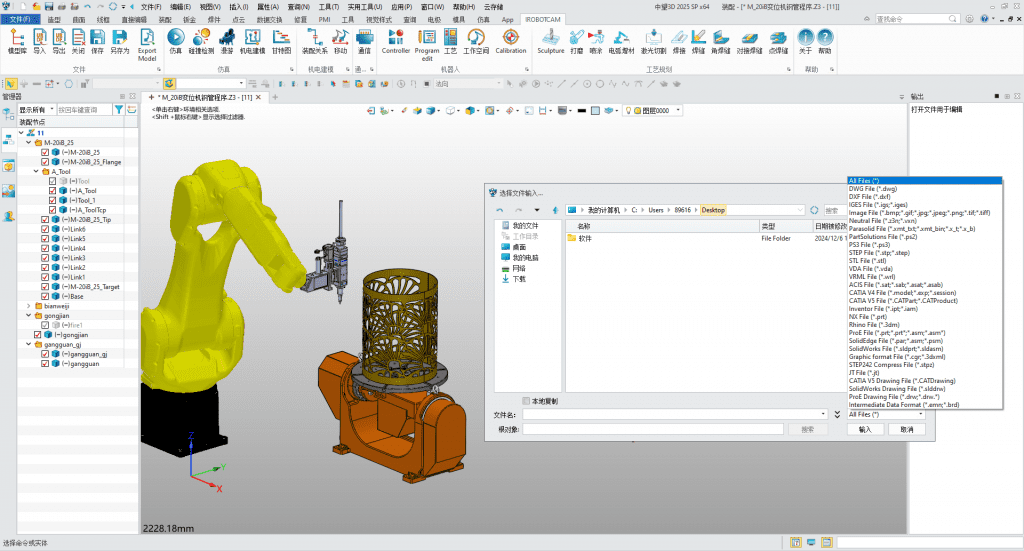
Cost and benefit level
- Reduce development costs: As a domestic software developed based on Zhongwang 3D platform, its product architecture is open and expandable. Compared with similar foreign software, it may have certain advantages in purchase cost and follow-up maintenance cost. At the same time, its efficient programming and debugging functions can reduce the time cost of manual programming and debugging, and indirectly reduce the development cost of enterprises.
- Improve equipment utilization: Through accurate trajectory planning and virtual debugging functions, you can ensure the stability and reliability of robots and laser equipment during processing, reduce equipment failures and downtime, and improve the utilization of equipment, thereby creating more economic benefits for enterprises.
User experience and service level
- Friendly operation interface: It usually has an intuitive and simple user operation interface, and even operators without rich programming experience can quickly get started, reducing the learning cost and use threshold of the software, and facilitating the use and management of technical personnel and operators within the enterprise.
- Reliable technical support: As the developer of iRobotCAM, iRobotCAM has a professional technical team, which can provide users with technical support and solutions in time to help users solve various problems encountered in the use process to ensure the stable operation of the software and the smooth progress of enterprise production.
About Yueqing Technology :
Yueqing Technology is committed to building an open iRobotCAM robot offline programming platform, which is a digital solution integrating electromechanical conceptual design of production lines, robot processing programming simulation, and virtual debugging.
iRobotCAM website: www.iRobotCAM.com,contact: cooperation@iRobotCAM.com