Abstract: Aiming at the application scenarios of robot material unit automation, iRobotCAM, a domestic robot offline programming software developed by YueQing Technology, provides a convenient material unit design module, which can quickly establish communication with PLC and realize automation according to the needs of material units.
As the basis for the design and simulation debugging of a robot production line, the material production unit has derived design methods for various different components in a convenient way. Returning to the source, from the perspective of the overall material flow, the process of most basic material scenarios is similar to the following mode:
- In the scene, the conveyor belt entrance produces materials, transports materials to the end, senses the materials at the end, and the conveyor belt stops running.
- The robot in the loading area obtains the signal to clamp the material to the machine tool for processing and loading, and finally places it on the conveyor plate for transportation.
- The robot in the unloading area waits for the conveyor plate to transport the material out, and after obtaining the signal, clamps the material to the material placement table.
- The conveyor belt entrance continues to produce materials, and the robot enters the cycle of loading and unloading.
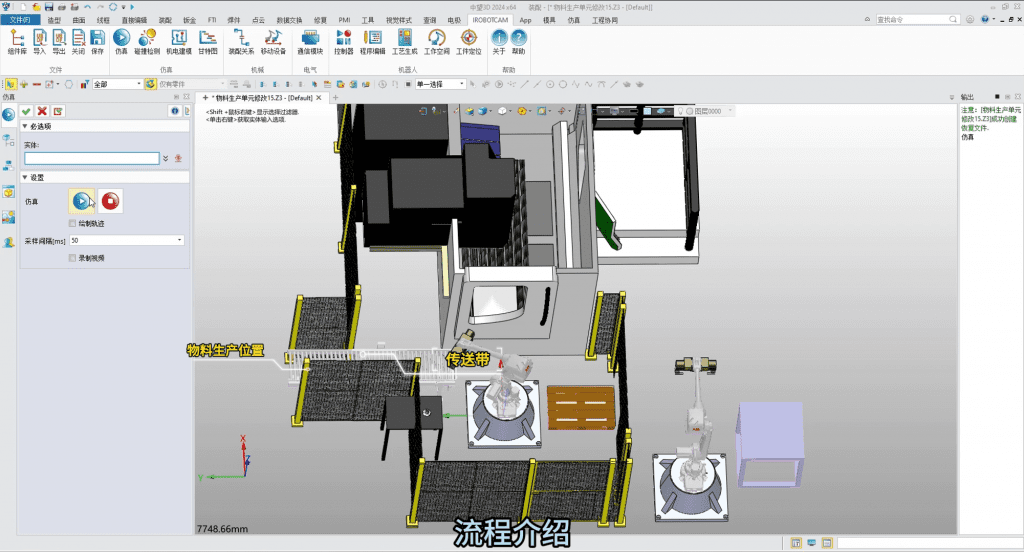
The function design is highly convenient. The material unit is capable of automatically generating materials for diverse production lines. The function window of the material production unit is established by incorporating production objects, production locations, and production frequencies.
Its function expansion capacity is remarkable. Specifically tailored to the requirements of the material unit, iRobotCAM’s powerful physical engine can fulfill the demands of multi-robot motion simulation even in more intricate scenarios.
Take the application of robot loading and unloading as an instance. iRobotCAM can promptly implement the following designs:
Firstly, import the robot model into the scene from the component library and assemble it to the robot by separately setting the robot tools.
Secondly, the software enables the addition of markers through drag-and-drop teaching, along with the addition of robot program instructions, thereby controlling the robot program to execute the loading and unloading functions.
Finally, multiple robots can be added to the scene, and the robot program instructions are managed by the multi-robot controller to carry out the loading and unloading area functions respectively.
As a material production unit, we will further explore how iRobotCAM conveniently achieves the automation of the robot material unit via the following video.
About Yueqing Technology
Yueqing Technology is committed to building an open iRobotCAM robot offline programming platform, which is a digital solution integrating electromechanical conceptual design of production lines, robot processing programming simulation, and virtual debugging.
iRobotCAM website: www.iRobotCAM.com; Contact: cooperation@iRobotCAM.com