Abstract: The means of surface quality inspection of products vary, and the main goal is to achieve more efficient automated inspection. With the improvement of robot accuracy and stability, the automated inspection of robots is becoming more and more widely used. As a representative of domestic robot offline programming software, iRobotCAM uses iRobotCAM’s friendly programming process to achieve robot automated inspection through fast programming and simulation.
The process of industrial robots is applied in various fields such as welding, laser processing, grinding, spraying, and additive manufacturing. On the basis of the application of multiple processes, the detection of surface quality often still requires a lot of manual inspection due to the specific application scenarios involved, and the core application obstacle is actually the most basic accuracy problem. One is the accuracy of the robot itself, and the other is the accuracy of the detection software itself.
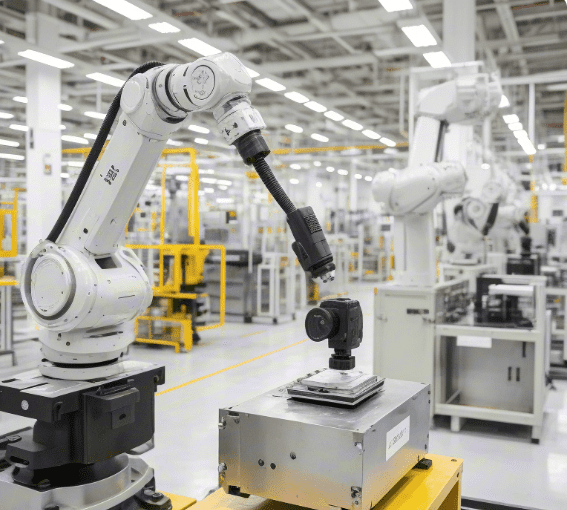
On the basis of greatly improved precision and reliability of industrial robots, iRobotCAM takes advantage of the research and development of 3D geometric modeling kernel to ensure high-precision requirements in product architecture, thereby meeting the needs of robot processing and robot detection at the same time.
More specifically, as the first robot offline programming and simulation software developed based on the domestic three-dimensional geometric kernel, how can iRobotCAM provide an efficient solution for the needs of robot automated detection?
- Taking advantage of the CAD architecture based on the three-dimensional geometric kernel, iRobotCAM can achieve high-precision trajectory programming and realize the precision control needs of robot automated detection.
2. Using iRobotCAM’s robot library, you can quickly add the required robot models, product models, etc. to the digital scene, and quickly realize programming and verification.
3. Taking advantage of iRobotCAM’s open process architecture and reliable physical engine, iRobotCAM has various process applications such as robot welding, spraying, laser cutting, arc additive, 3D printing, engraving, polishing and grinding, which can quickly unify robot processing and robot detection software, and efficiently improve the automation of robot programming and detection.
Next, let’s take a look at how iRobotCAM can easily realize the programming and simulation of robot inspection.
About Yueqing Technology
Yueqing Technology is committed to building an open iRobotCAM robot offline programming platform, which is a digital solution integrating electromechanical conceptual design of production lines, robot processing programming simulation, and virtual debugging.
iRobotCAM website: www.iRobotCAM.com; Contact: cooperation@iRobotCAM.com