Abstract: Robot laser processing is increasingly used, and the rapid programming and simulation of robot processing technology can easily verify the correctness of the process. As the representative of domestic robot offline programming software, iRobotCAM, using iRobotCAM’s friendly programming process, can achieve For process programming and simulation verification, it further provides the convenience of machining laser processing.
The birth of any processing technology is to solve certain types of problems in industrial applications. The application of laser is becoming more and more widespread, mainly because when the energy of laser is controllable, more complex processing technology can be realized, so that it can be used in various types of simple two-axis to five-axis laser cutting, or more complex aviation and other parts. The field of laser welding further meets the process needs of various types of parts. In order to make better use of robotic laser processing, in addition to the hardware capabilities of the laser itself, further requirements are put forward for the convenience and accuracy of process generation trajectories and simulations.
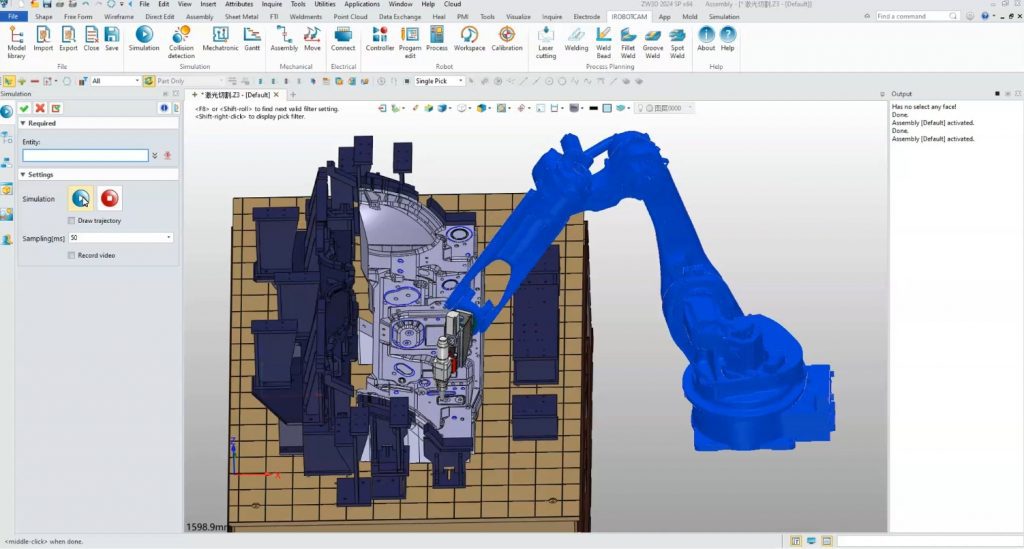
For robotic laser processing, taking the difficulties in laser cutting technology as an example, there are mainly the following
- Low positioning and correction efficiency and poor adaptability: Line laser positioning or resistor positioning methods have their limitations. The line laser intersection is susceptible to interference, and resistor positioning has requirements for the placement of the workpiece. Positioning and correction If there is any deviation in the placement of the workpiece, it is easy to fail in positioning. For large or complex workpieces, all edges need to be scanned one by one, which is less efficient. And these methods usually only provide local position correction, and have poor adaptability to arc-shaped special-shaped parts.
- Robot trajectory planning: Although robot trajectory programming is flexible, in some complex or delicate cutting tasks, how to optimize the robot’s motion trajectory to improve cutting efficiency and quality is still a challenge.
- Equipment maintenance and calibration: Laser cutting robots involve multiple precision components, such as laser emitters, sensors, and robotic arms. Maintenance and calibration of these components is critical to maintaining cutting accuracy and extending equipment life. However, how to perform regular maintenance and calibration, and how to quickly respond to equipment failures are all issues that need to be faced in the robotic laser cutting process.
As a robot offline programming and simulation software, iRobotCAM targets the process requirements of robot laser processing and is based on its research and development accumulation in the welding field in the past ten years.
- Utilizing the scalability of the three-dimensional CAD platform, the automation of the extraction of laser welding trajectories is realized, and the precise control of the laser trajectories is further achieved.
- Utilizing years of experience in the research and development of robot physics engines, we can quickly realize the simulation of robot laser processes and realize the digital twin of the machining process.
- Using iRobotCAM’s trajectory generation and trajectory optimization modules, the robot’s trajectory can be automatically adjusted to avoid collisions, singular points and unreachable points.
- By combining iRobotCAM’s production line design with robot programming and simulation, iRobotCAM may realize production line-level design and simulation, achieving integration of design and simulation.
Let’s take a look at how iRobotCAM can easily implement programming and simulation of robot laser processing.
About Yueqing Technology :
Yueqing Technology is committed to building an open iRobotCAM robot offline programming platform, which is a digital solution integrating electromechanical conceptual design of production lines, robot processing programming simulation, and virtual debugging.